Sorry, this content is for members only.
Join To View ThisRelated Post: 3D Printed Metal Space Fabric / High Definition 3D Printing / 3D Printed Aluminum
Ganit Goldstein is a 3D Textile and Fashion designer specializing in the development of smart textile systems. Ganit’s primary interest is in the intersection between craft and technology, combining virtual tools and tangible materials to extend the possibilities of programmable textiles. Her work focuses predominantly on pioneering the use of 3D printing fabrication to produce customized 3D textiles.
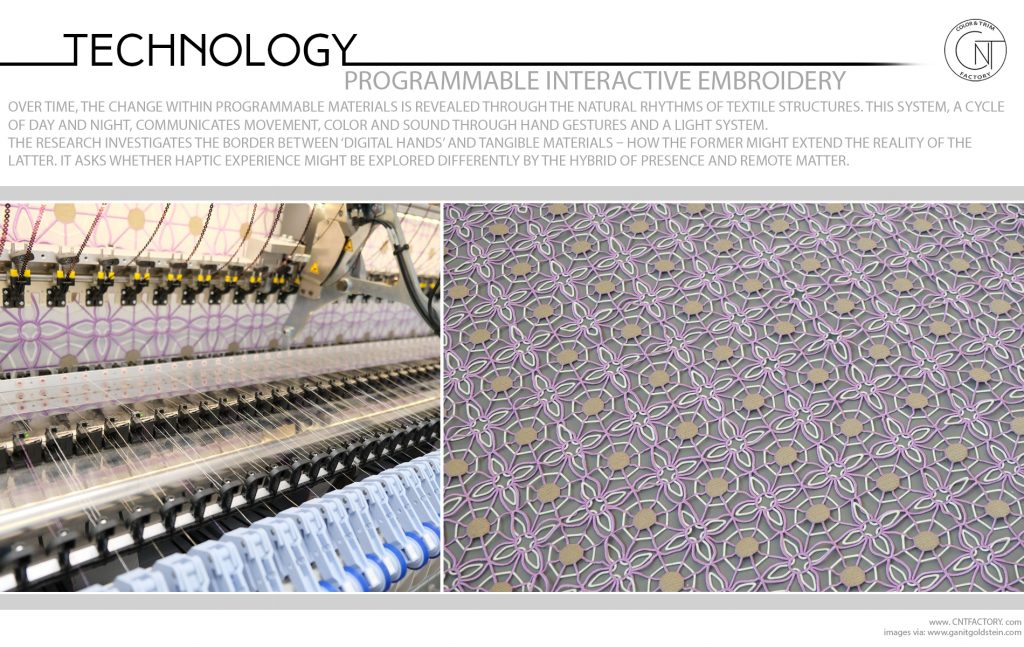
Over time, the change within programmable materials is revealed through the natural rhythms of textile structures. This system, a cycle of day and night, communicates movement, color and sound through hand gestures and a light system. The research investigates the border between ‘digital hands’ and tangible materials – how the former might extend the reality of the latter. It asks whether haptic experience might be explored differently by the hybrid of presence and remote matter.
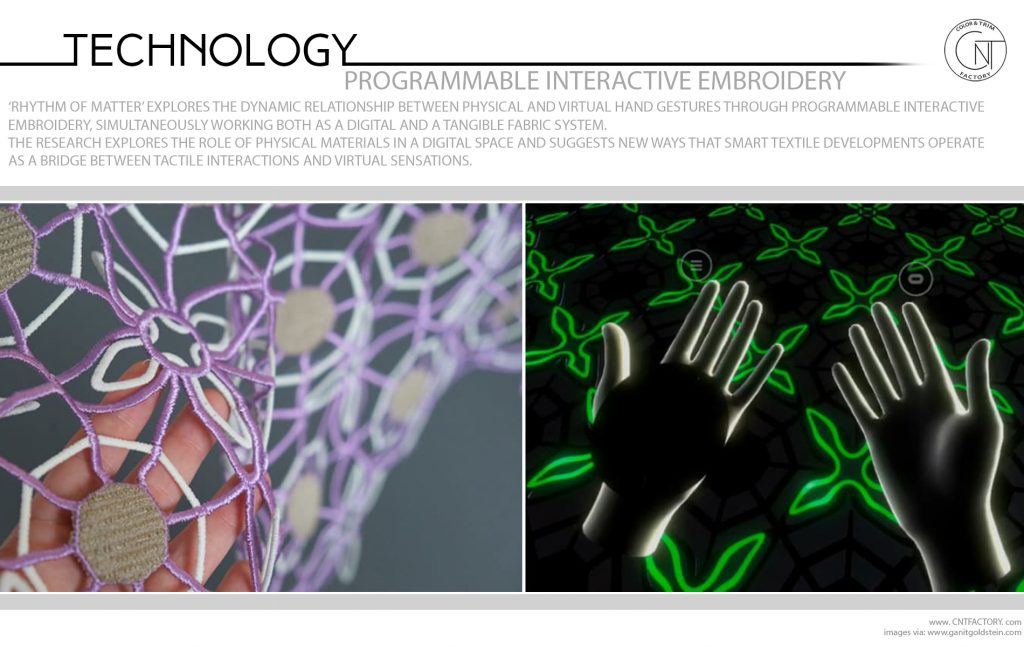
‘Rhythm of Matter’ explores the dynamic relationship between physical and virtual hand gestures through programmable interactive embroidery, simultaneously working both as a digital and a tangible fabric system.
The research explores the role of physical materials in a digital space and suggests new ways that smart textile developments operate as a bridge between tactile interactions and virtual sensations.
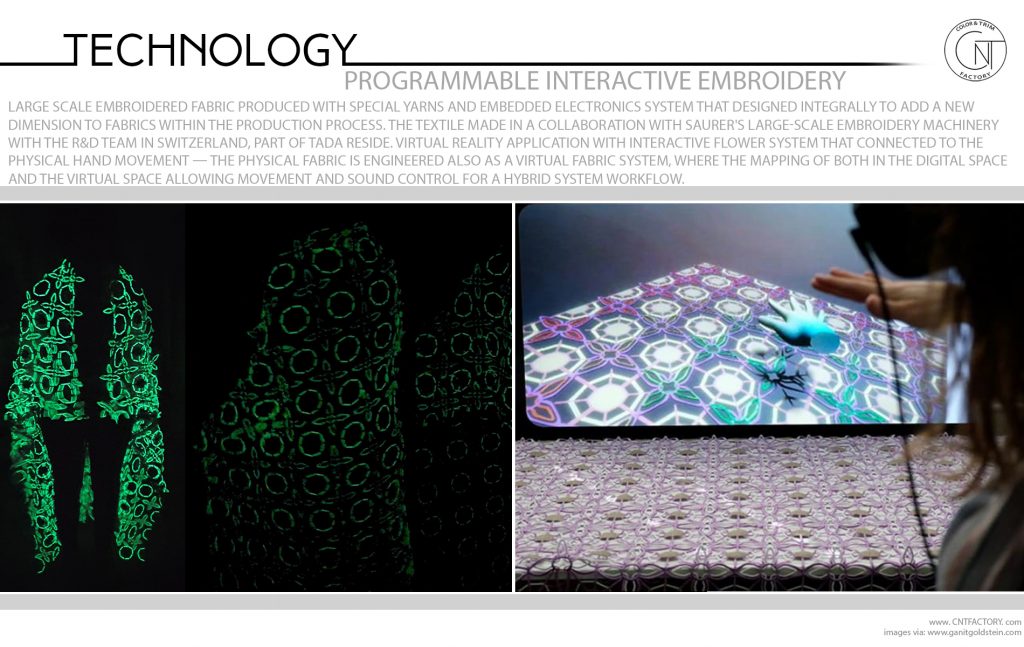
Large scale embroidered fabric produced with special yarns and embedded electronics system that designed integrally to add a new dimension to fabrics within the production process. The textile made in a collaboration with Saurer’s large-scale embroidery machinery with the R&D team in Switzerland, part of TaDA reside. Virtual Reality application with interactive flower system that connected to the physical hand movement. The physical fabric is engineered also as a virtual fabric system, where the mapping of both in the digital space and the virtual space allowing movement and sound control for a hybrid system workflow.
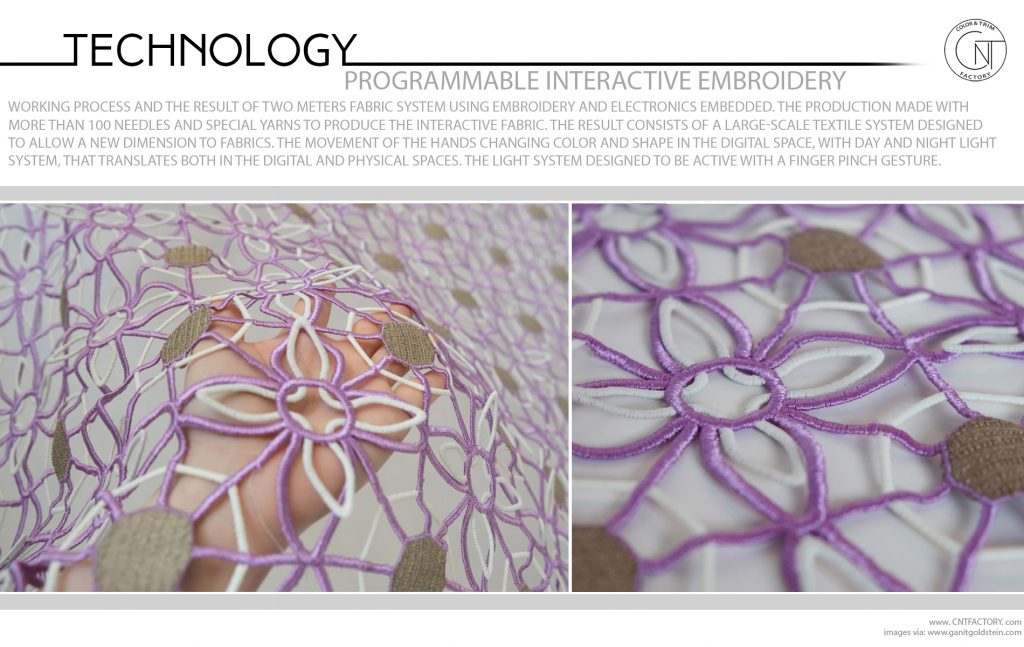
Working process and the result of two meters fabric system using embroidery and electronics embedded. The production made with more than 100 needles and special yarns to produce the interactive fabric. The result consists of a large-scale textile system designed to allow a new dimension to fabrics.
The movement of the hands changing color and shape in the digital space, with day and night light system, that translates both in the digital and physical spaces. The light system designed to be active with a finger pinch gesture.