Sorry, this content is for members only.
Join To View ThisRelated Post: Space Fabric / BMW Vision iNEXT / Puma x BMW X-Cat Disc
A new study led by Philipp Kürnsteiner of the Max Planck Institute for Iron Research shows that it is possible to do something very similar with laser additive manufacturing – 3D printed metals.
Traditional folded steels combined two steels that varied by carbon content and in their microscale structure, which is controlled by how quickly it cools (by quenching). In this case, the researchers were using a nickel-titanium-iron alloy steel that works well with these 3D printing techniques, in which metal powder is fed onto the work surface and heated with a laser.
Rapid cooling of this steel also produces a crystalline form as in quenched high-carbon steels. But further heat treatment leads to the precipitation of microscopic nickel-titanium particles within the steel that greatly increase its hardness – a pricey material called “maraging steel.”
Damascus steel jewellery is often mentioned together with the Mokume Gane design since it also comes with a layered and bonded pattern. As the name implies, damascus steel rings are of steel construction and are not as costly to produce as Mokume Gane. They are made by layering steel shades of silver and gray and heat bonding in an oxygen free environment.
Mokume Gane is created by layering and bonding metals of different colors. A Mokume Gane ring can include gold, silver, copper and platinum. Mokume Gane rings are generally one off piece as pattern replication is near impossible.
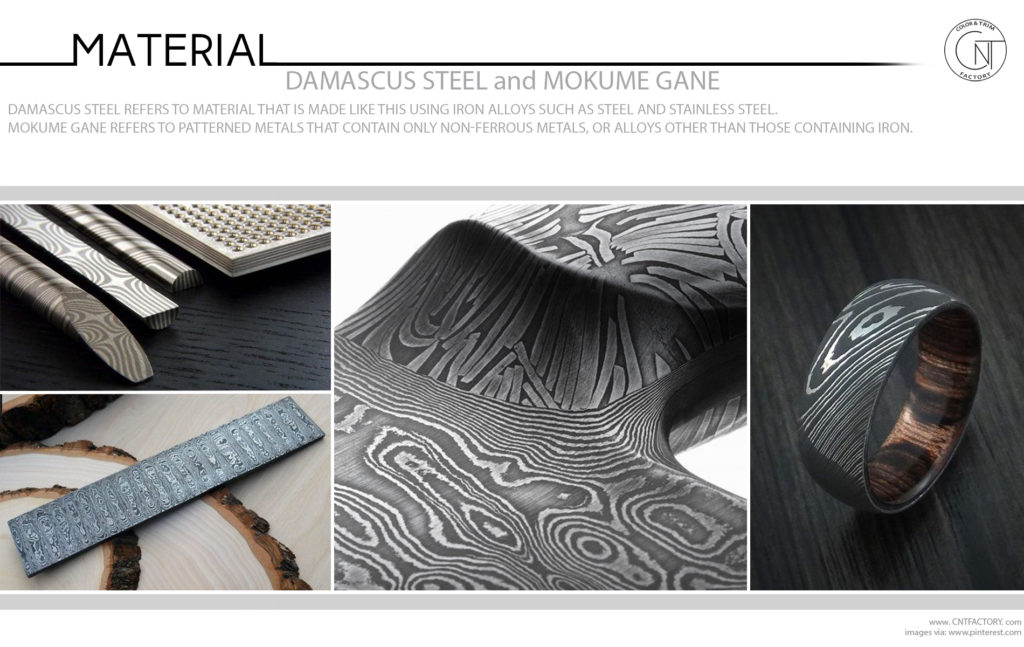
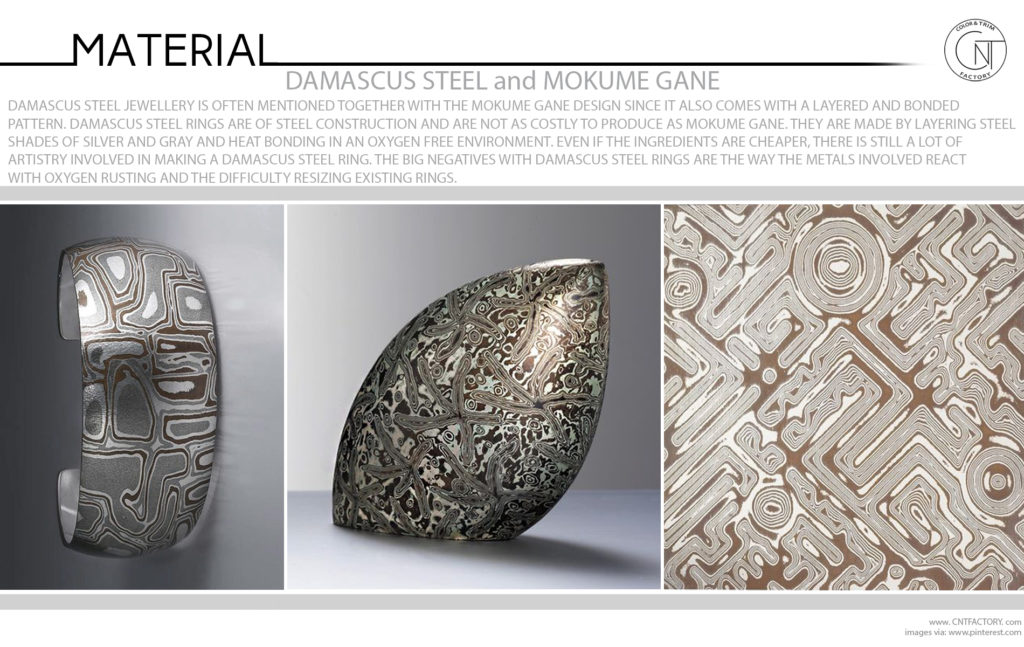
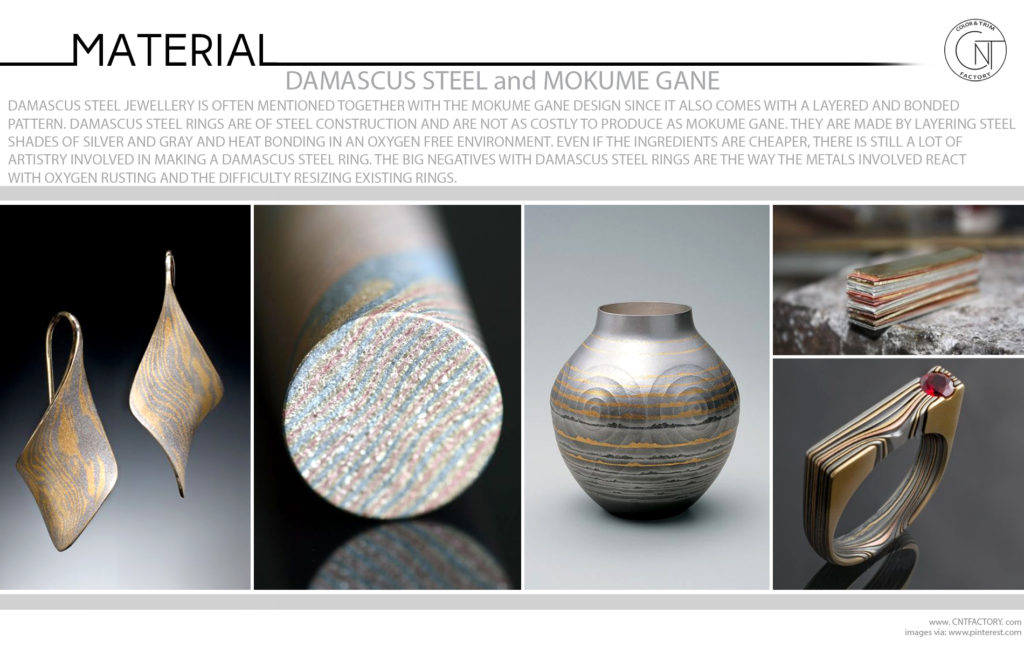
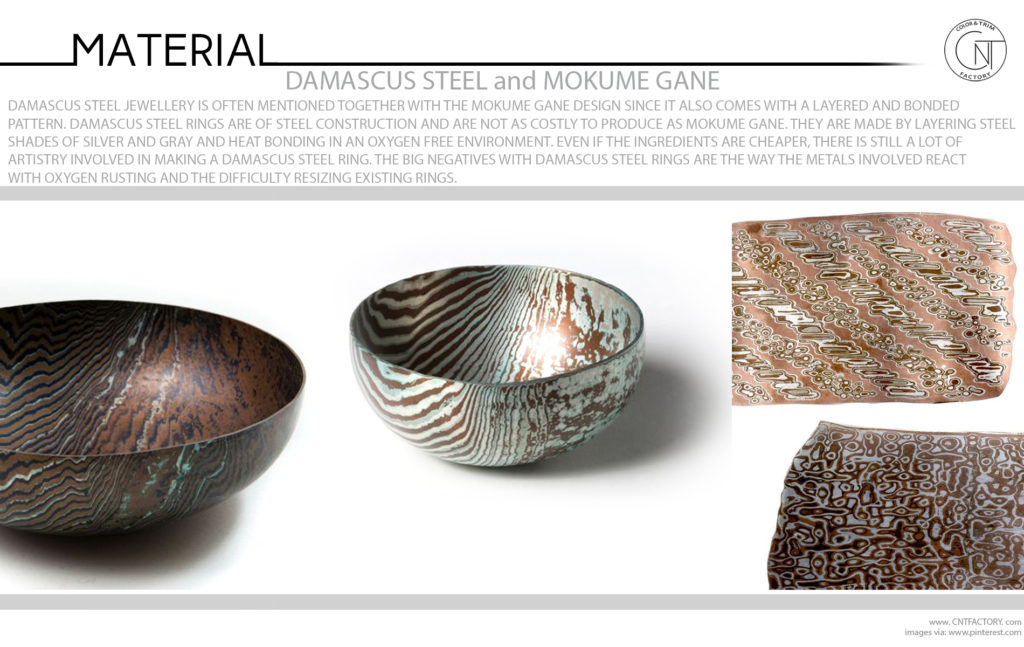